Piezoelectric Energy Harvesting
Piezoelectric Energy Harvesting:
Airplanes have become a common form of transportation in the modern world. In a single airplane miles and miles of wiring is used to power the many instrumentation sensors that make an airplane functional and safe. The wiring is complicated and contributes to the weight of the airplane. Piezoelectric energy harvesting is a possible solution to eliminate aircraft wiring, especially in testing. Via the piezoelectric effect, aerodynamic vibrations are transformed into usable electrical power to supply small sensors and wireless nodes.

Piezoelectric Effect:
Piezoelectricity is produced from the deformation of certain types of crystals and ceramics. The deformation can be caused by pressure or vibration. This process of creating electricity from mechanical forces is called the piezoelectric effect.
Piezoelectric Energy Harvesters (PEHs) use this process to take mechanical energy from the surrounding environment and convert it to electrical energy. In our research the PEH harvests ambient vibration from the airplane environment (possibly in the wing), and converts that energy to usable electrical voltage. That voltage can then be used to power other sensors.
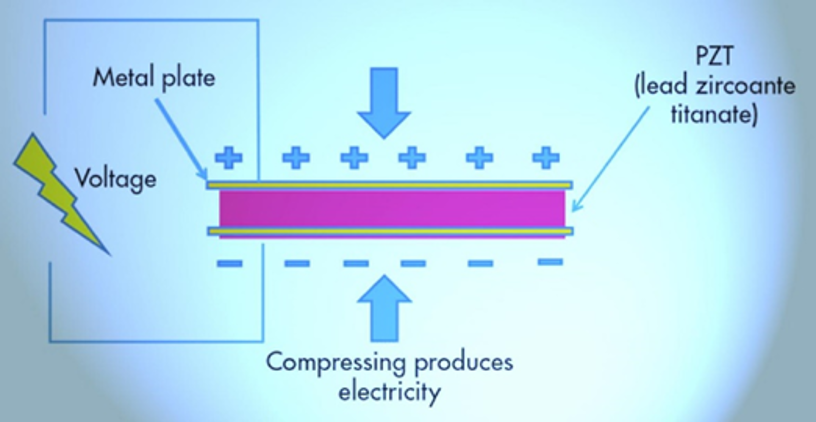
Our Contributions:
We are looking into the possibility of using piezoelectric energy harvesters to provide power to small transducers, like a strain gauge. Our research includes mathematical models for a piezoelectric cantilever, and experiments using piezo discs.

Cantilever Mathematical Modeling:
The goal is to produce energy harvesters that can take the the aerodynamic vibrations and produce electrical energy. After reviewing multiple energy harvesting geometries, we decided to mathematically model the simplest configuration of vibration harvester, a unimorph composite beam. It consists of a sheet of piezoelectric material bonded to an aluminum supportive layer that is fixed on one end.
We completed derivations to determine the voltage, current and power relationships.
The mathematical and analytical model resulted in the following conclusions:
- We can change the resonant frequency of the cantilever beam by changing the length of the beam
- Peak voltage, current and power occur at low frequencies and high intensities

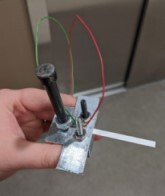
Experimental Analysis:
We first tested the accuracy of the mathematical models with a piezoelectric beam. We made a mounting fixture to anchor the piezo beam on one end. We conducted a test for the resonance frequency. The results were similar to the analytical models of resonance frequency modes.
Our experimental analysis is ongoing. We are looking into the power output of a piezo disc, a component used in various applications. The piezo disc is fastened to a mechanical fixture, which is then mounted to a shaker. The shaker provides the mechanical excitation to the piezo disc, which acts much like a beam since it is fixed on one end. The excitation is converted to electrical current which moves through an AC-DC rectifier so the harvested energy can be used to power a DC transducer.
In the future we hope to experiment powering a common airplane transducer, the strain gauge, with a single PEH.


Future Work:
- Powering a transducer load
- Cantilever Geometry Optimization
- Cantilever Arrays